Factory Layout
A factory layout is a schematic that shows all the internal part of the structure that make up the entire factory. this is integral to a factory's production due to being able to determine or create the areas where people, materials, equipment and everything will be in and out.
Some of the important types of plant layout are: A. Product or line layout, B. Process or functional layout, C. Layout by stationary material!
have to be maintained.
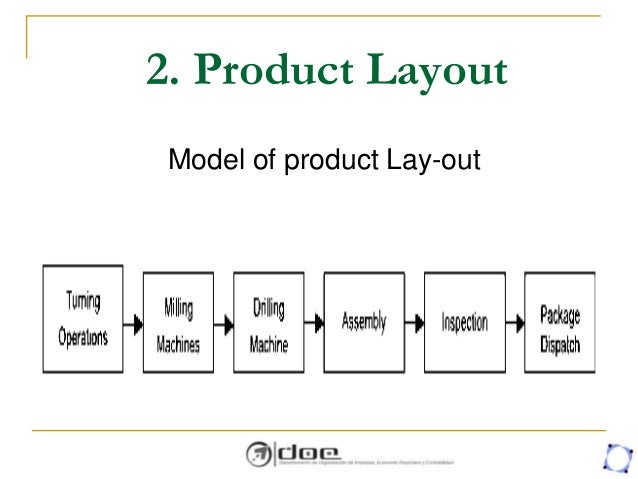
Product layout ensures unrestricted and continuous production thereby minimising bottlenecks in the process of production, this is because work stoppages are minimum under this method.
(2) Economies in material handling:
Under this method there are direct channels for the flow of materials requiring lesser time which considerably eliminate back-tracking of materials. On account of this, cost of material handling is considerably reduced. This is greatly helpful in achieving desired quality of the end product.
3) Lesser manufacturing time:
Under this method (as already pointed), backward and forward handling of materials is not involved, it leads to considerable saving in manufacturing time.
(4) Lesser work in progress:
On account of continuous uninterrupted mass production, there is lesser accumulation of work in progress or semi-finished goods.
(5) Proper use of floor space:
This method facilitates proper and optimum use of available floor space. This is due to non- accumulation of work in progress and overstocking of raw materials.
(6) Economy in inspection:
Inspection can be easily and conveniently undertaken under this method and any defect in production operations can be easily located in production operations. The need for inspection under this method is much less and can be confined at some crucial points only.
(7) Lesser manufacturing cost:
On account of lesser material handling, inspection costs and fullest utilisation of available space, production costs are considerably reduced under this method.
(8) Lesser labour costs:
Due to specialisation and simplification of operations and use of automatic simple machines, employment of unskilled and semi-skilled workers can carry on the work. The workers are required to carry routine tasks under this method. This leads to lesser labour costs.
(9) Introduction of effective production control:
Effective production control on account of simple operation of this method can be employed successfully. Production control refers to the adoption of measures to achieve production planning.
As work is carried in sequence and process arranged in a line, it is very difficult to make adjustments in production of operations. Sometimes, certain changes under this method become very costly and impractical. On account of this drawback, this method is not suitable in the production of goods which are subject to quick style and design changes.
(2) Large investment:
Under this method, machines are not arranged in accordance with functions as such similar type of machines and equipment is fixed at various lines of production. This leads to unavoidable machinery duplication resulting in idle capacity and large capital investment on the part of the entrepreneur.
(3) Higher overhead charges:
Higher capital investment leads to higher overheads (fixed overheads) under this method. This leads to excessive financial burden.
(4) Interruption due to breakdown:
If one machine in the sequence stops on account of breakdown, other machines cannot operate and work will be stopped. The work stoppage may also take place on account of irregular supply of material, poor production scheduling and employee absenteeism etc.
(5) Difficulties in expanding production:
Production cannot be expanded beyond certain limits under this method.
(6) Lack of specialisation in supervision:
Supervision of different production jobs becomes difficult under this method as there is absence of specialised supervision as the work is carried on in one line having different processes and not on the basis of different departments for different specialised jobs. Under this method a supervisor is supposed to have detailed knowledge of all the machines and processes which leads to absence of specialisation in the process of supervision.
(7) Under-utilisation of machines:
As has already been pointed out, separate set of one type of machines is fixed at different lines of production. Usually, these machines are not properly and fully utilised and there remains idle capacity in the form of under utilised equipment.
This method is generally adopted for producing different varieties of unlike products. This is particularly adopted tor job order industries like engineering, ship building and printing etc. The following diagram shows that raw material travels through various process or departments from lathes passing through mills, grinders, drills, welding, inspection, finishing, and assembly and to finished product.
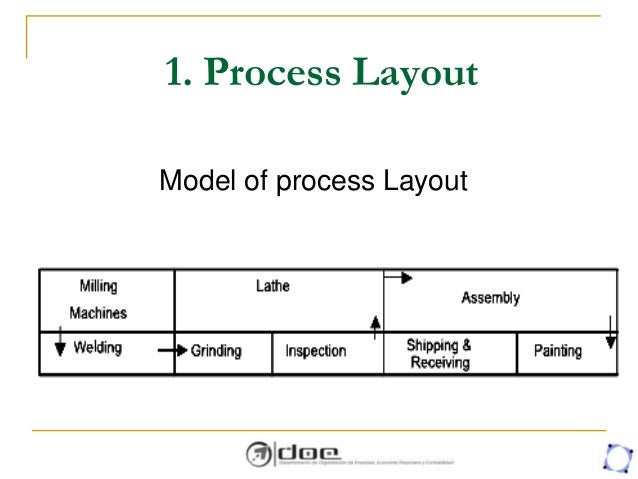
This method ensures fuller and effective utilisation of machines and consequently investment in equipment and machines becomes economical.
(2) Greater flexibility:
Changes in the sequence of machines and operations can be made without much difficulty. This is because the machines are arranged in different departments in accordance with the nature of functions performed by them.
(3) Scope for expansion:
Production can be increased by installing additional machines without much difficulty.
(4) Specialisation:
As has already been pointed out that under this method, specialised machines are used for performing different production operations. This leads to specialisation.
(5) Effective utilisation of workers:
Specialised workers are appointed to carry different type of work in different departments. This leads to effective and efficient use of their talent and capabilities.
(6) More effective supervision:
As the machines are arranged on the basis of functions, performed by them, the specialised and effective supervision is ensured by the specialised knowledge of supervisors. Each supervisor can perform his task of supervision effectively as he has to supervise limited number machines operating in his department.
(7) Lesser work stoppages:
Unlike the product method, if a machine fails, it does not lead to complete work stoppage and production schedules are not seriously affected. Due to breakdown in one machine, the work can be easily transferred to the other machines.
Under this method, more floor space is needed for the same quantum of work as compared to product layout.
(2) Higher cost of material handling:
Material moves from one department to another under this method, leading to the higher cost of material handling. The mechanical devices of material handling cannot be conveniently employed under this method on account of functional division of work. Material has to be carried by applying other methods from one department to another, resulting into higher cost of material handling.
(3) Higher labour costs:
As there is functional division of work, specialised workers are to be appointed in different departments for carrying specialised operations. The appointment of skilled worker leads to higher labour costs.
(4) Longer production time:
Production takes longer time for completion under this method and this leads to higher inventories of work-in-progress.
(5) Difficulties in production, planning and control:
Due to large variety of products and increased size of the plant, there are practical difficulties in bringing about proper coordination among various areas (departments) and processes of production. The process of production, planning and control becomes more complex and costly.
(6) Increased inspection costs:
Under this type of layout more supervisors are needed and work is to be checked after every operation which makes the process of supervision costlier.
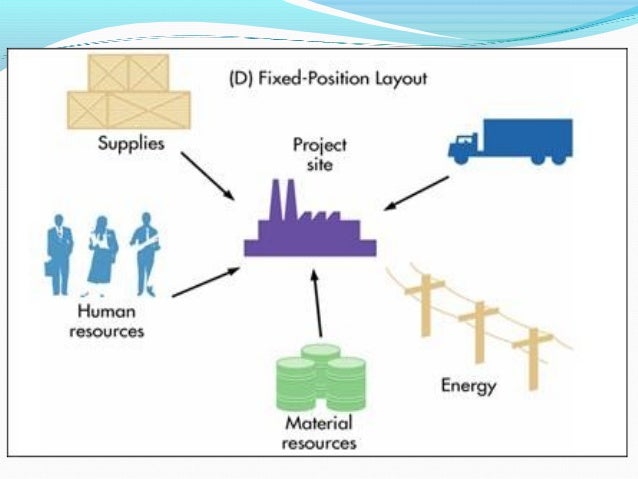
As the work is carried at one place and material is not taken from one place to another, this leads to savings in transformation costs.
(b) Different jobs with same layout:
Different projects can be undertaken with the help of same layout.
(c) Production in accordance with specifications:
The jobs can be performed in accordance with the specifications given by the customers.
(d) Scope for flexibility:
It provides maximum flexibility for various changes in production processes and designs of the products.
As material is fixed at one place, this leads to certain difficulties in arranging specialised workers, machines and equipment for the job.
(b) Large investment:
This method is time consuming and costlier as compared to first two methods.
(c) Unsuitable for small products:
This method is not suitable for producing and assembling small products in large quantities. In actual practice, it has been observed that a judicious combination of three types’ viz., product, process and stationary material layout is undertaken by different organisations. This is done with the view to enjoy the advantages of all the methods.
Some of the important types of plant layout are: A. Product or line layout, B. Process or functional layout, C. Layout by stationary material!
(A) Product or Line Layout:
Product or Line Layout is the arrangement of machines in a line (not always straight) or a sequence in which they would be used in the process of manufacture of the product. This type of layout is most appropriate in case of continuous type of industries where raw materials is fed at one end and taken out as finished product at the other end. For each type of product a separate line of production willhave to be maintained.
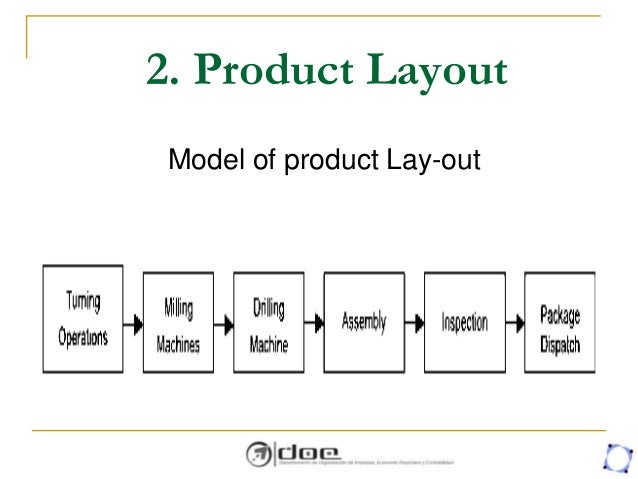
Advantages of Product Layout:
(1) Removal of obstacles in production:Product layout ensures unrestricted and continuous production thereby minimising bottlenecks in the process of production, this is because work stoppages are minimum under this method.
(2) Economies in material handling:
Under this method there are direct channels for the flow of materials requiring lesser time which considerably eliminate back-tracking of materials. On account of this, cost of material handling is considerably reduced. This is greatly helpful in achieving desired quality of the end product.
3) Lesser manufacturing time:
Under this method (as already pointed), backward and forward handling of materials is not involved, it leads to considerable saving in manufacturing time.
(4) Lesser work in progress:
On account of continuous uninterrupted mass production, there is lesser accumulation of work in progress or semi-finished goods.
(5) Proper use of floor space:
This method facilitates proper and optimum use of available floor space. This is due to non- accumulation of work in progress and overstocking of raw materials.
(6) Economy in inspection:
Inspection can be easily and conveniently undertaken under this method and any defect in production operations can be easily located in production operations. The need for inspection under this method is much less and can be confined at some crucial points only.
(7) Lesser manufacturing cost:
On account of lesser material handling, inspection costs and fullest utilisation of available space, production costs are considerably reduced under this method.
(8) Lesser labour costs:
Due to specialisation and simplification of operations and use of automatic simple machines, employment of unskilled and semi-skilled workers can carry on the work. The workers are required to carry routine tasks under this method. This leads to lesser labour costs.
(9) Introduction of effective production control:
Effective production control on account of simple operation of this method can be employed successfully. Production control refers to the adoption of measures to achieve production planning.
Disadvantages of Product Layout:
(1) Lesser flexibility:As work is carried in sequence and process arranged in a line, it is very difficult to make adjustments in production of operations. Sometimes, certain changes under this method become very costly and impractical. On account of this drawback, this method is not suitable in the production of goods which are subject to quick style and design changes.
(2) Large investment:
Under this method, machines are not arranged in accordance with functions as such similar type of machines and equipment is fixed at various lines of production. This leads to unavoidable machinery duplication resulting in idle capacity and large capital investment on the part of the entrepreneur.
(3) Higher overhead charges:
Higher capital investment leads to higher overheads (fixed overheads) under this method. This leads to excessive financial burden.
(4) Interruption due to breakdown:
If one machine in the sequence stops on account of breakdown, other machines cannot operate and work will be stopped. The work stoppage may also take place on account of irregular supply of material, poor production scheduling and employee absenteeism etc.
(5) Difficulties in expanding production:
Production cannot be expanded beyond certain limits under this method.
(6) Lack of specialisation in supervision:
Supervision of different production jobs becomes difficult under this method as there is absence of specialised supervision as the work is carried on in one line having different processes and not on the basis of different departments for different specialised jobs. Under this method a supervisor is supposed to have detailed knowledge of all the machines and processes which leads to absence of specialisation in the process of supervision.
(7) Under-utilisation of machines:
As has already been pointed out, separate set of one type of machines is fixed at different lines of production. Usually, these machines are not properly and fully utilised and there remains idle capacity in the form of under utilised equipment.
B) Functional or Process Layout:
It is just the reverse of product layout. There is a functional division of work under this method. For example, lathes are fixed in one department and welding activities are carried in another department of the factory. The salient features of this type of layout are based on Frederick W. Taylor’s concept of ‘functional organisation’.This method is generally adopted for producing different varieties of unlike products. This is particularly adopted tor job order industries like engineering, ship building and printing etc. The following diagram shows that raw material travels through various process or departments from lathes passing through mills, grinders, drills, welding, inspection, finishing, and assembly and to finished product.
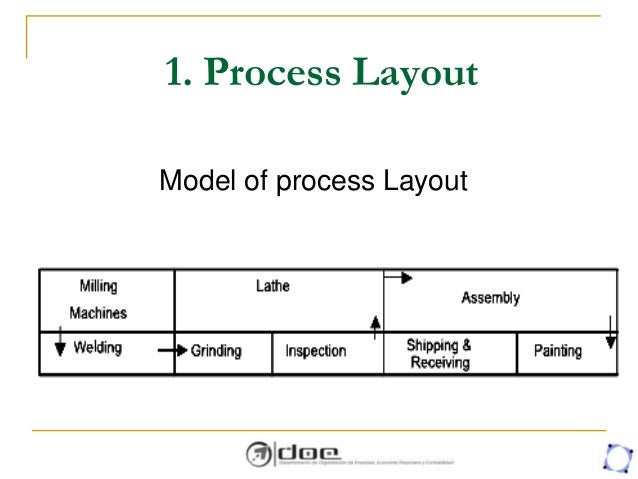
Advantages of Process Layout:
(1) Maximum utilisation of machines:This method ensures fuller and effective utilisation of machines and consequently investment in equipment and machines becomes economical.
(2) Greater flexibility:
Changes in the sequence of machines and operations can be made without much difficulty. This is because the machines are arranged in different departments in accordance with the nature of functions performed by them.
(3) Scope for expansion:
Production can be increased by installing additional machines without much difficulty.
(4) Specialisation:
As has already been pointed out that under this method, specialised machines are used for performing different production operations. This leads to specialisation.
(5) Effective utilisation of workers:
Specialised workers are appointed to carry different type of work in different departments. This leads to effective and efficient use of their talent and capabilities.
(6) More effective supervision:
As the machines are arranged on the basis of functions, performed by them, the specialised and effective supervision is ensured by the specialised knowledge of supervisors. Each supervisor can perform his task of supervision effectively as he has to supervise limited number machines operating in his department.
(7) Lesser work stoppages:
Unlike the product method, if a machine fails, it does not lead to complete work stoppage and production schedules are not seriously affected. Due to breakdown in one machine, the work can be easily transferred to the other machines.
Disadvantages of Process Layout:
(1) Coverage of more floor area:Under this method, more floor space is needed for the same quantum of work as compared to product layout.
(2) Higher cost of material handling:
Material moves from one department to another under this method, leading to the higher cost of material handling. The mechanical devices of material handling cannot be conveniently employed under this method on account of functional division of work. Material has to be carried by applying other methods from one department to another, resulting into higher cost of material handling.
(3) Higher labour costs:
As there is functional division of work, specialised workers are to be appointed in different departments for carrying specialised operations. The appointment of skilled worker leads to higher labour costs.
(4) Longer production time:
Production takes longer time for completion under this method and this leads to higher inventories of work-in-progress.
(5) Difficulties in production, planning and control:
Due to large variety of products and increased size of the plant, there are practical difficulties in bringing about proper coordination among various areas (departments) and processes of production. The process of production, planning and control becomes more complex and costly.
(6) Increased inspection costs:
Under this type of layout more supervisors are needed and work is to be checked after every operation which makes the process of supervision costlier.
(C) Layout by position :
This type of layout is undertaken for the manufacture of large parts and assemblies. In this case, material remains fixed or stationary at one place, men and equipment are taken to the site of material. This is suitable in case of ship building, locomotives and heavy machinery industries etc.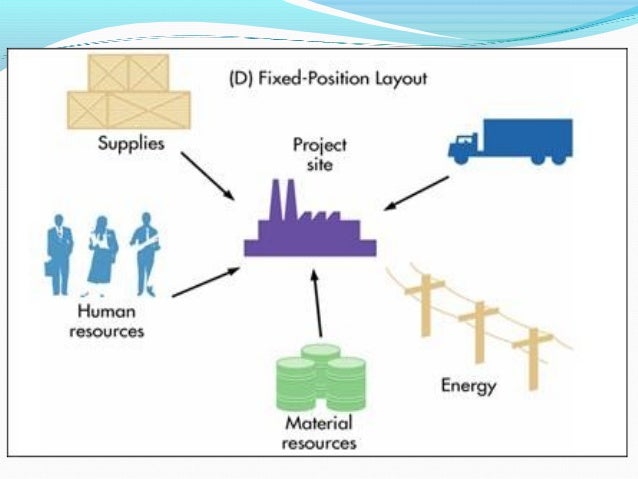
Advantages:
(a) Economies in transformation:As the work is carried at one place and material is not taken from one place to another, this leads to savings in transformation costs.
(b) Different jobs with same layout:
Different projects can be undertaken with the help of same layout.
(c) Production in accordance with specifications:
The jobs can be performed in accordance with the specifications given by the customers.
(d) Scope for flexibility:
It provides maximum flexibility for various changes in production processes and designs of the products.
Disadvantages:
(a) Immobility of material:As material is fixed at one place, this leads to certain difficulties in arranging specialised workers, machines and equipment for the job.
(b) Large investment:
This method is time consuming and costlier as compared to first two methods.
(c) Unsuitable for small products:
This method is not suitable for producing and assembling small products in large quantities. In actual practice, it has been observed that a judicious combination of three types’ viz., product, process and stationary material layout is undertaken by different organisations. This is done with the view to enjoy the advantages of all the methods.
BalasHapusReliable and skilled factory inspections by HK Q.C. CENTER help businesses maintain high-quality production standards.
Factory Inspection